Los hormigones refractarios con bajo contenido de cemento se comparan con los hormigones refractarios tradicionales de cemento de aluminato. La cantidad de cemento añadido en los hormigones refractarios tradicionales de cemento de aluminato suele ser del 12-20%, y la cantidad de agua, del 9-13%. Debido a la alta cantidad de agua añadida, el material colado presenta muchos poros, es poco denso y presenta baja resistencia. Debido a la gran cantidad de cemento añadido, si bien se pueden obtener mayores resistencias a temperaturas normales y bajas, esta disminuye debido a la transformación cristalina del aluminato de calcio a temperaturas medias. Obviamente, el CaO introducido reacciona con SiO₂ y Al₂O₃ en el hormigonable, generando sustancias de bajo punto de fusión, lo que deteriora las propiedades del material a altas temperaturas.
Cuando se utiliza tecnología de polvo ultrafino, aditivos de alta eficiencia y gradación científica de partículas, el contenido de cemento del moldeable se reduce a menos del 8% y el contenido de agua se reduce a ≤7%, y se puede preparar y llevar a cabo un moldeable refractario de serie de bajo cemento. El contenido de CaO es ≤2,5%, y sus indicadores de rendimiento generalmente superan los de los moldeables refractarios de cemento de aluminato. Este tipo de moldeable refractario tiene buena tixotropía, es decir, el material mezclado tiene una forma determinada y comienza a fluir con una pequeña fuerza externa. Cuando se elimina la fuerza externa, mantiene la forma obtenida. Por lo tanto, también se denomina moldeable refractario tixotrópico. El moldeable refractario autofluyente también se denomina moldeable refractario tixotrópico. Pertenece a esta categoría. El significado preciso de los moldeables refractarios de serie de bajo cemento no se ha definido hasta ahora. La Sociedad Americana para Pruebas y Materiales (ASTM) define y clasifica los moldeables refractarios en función de su contenido de CaO.
La densidad y la alta resistencia son las características sobresalientes de los refractarios de baja viscosidad. Esto mejora la vida útil y el rendimiento del producto, pero también presenta problemas durante el horneado, ya que el vertido puede ocurrir fácilmente si no se tiene cuidado durante el horneado. El fenómeno de estallido puede requerir, como mínimo, un nuevo vertido o, en casos graves, poner en peligro la seguridad personal de los trabajadores. Por lo tanto, varios países han realizado diversos estudios sobre el horneado de refractarios de baja viscosidad. Las principales medidas técnicas son: mediante la formulación de curvas de horno razonables y la introducción de excelentes agentes antiexplosión, etc., esto puede lograr que el agua de los refractarios se elimine sin problemas sin causar otros efectos secundarios.
La tecnología de polvo ultrafino es la tecnología clave para los refractarios refractarios de series bajas en cemento (actualmente la mayoría de los polvos ultrafinos utilizados en cerámica y materiales refractarios están en realidad entre 0,1 y 10 µm, y funcionan principalmente como aceleradores de dispersión y densificadores estructurales. El primero hace que las partículas de cemento estén altamente dispersas sin floculación, mientras que el segundo hace que los microporos en el cuerpo vertido se llenen completamente y mejora la resistencia.
Los tipos de polvos ultrafinos más utilizados actualmente incluyen SiO₂, α-Al₂O₃, Cr₂O₃, etc. La superficie específica del micropolvo de SiO₂ es de aproximadamente 20 m₂/g y su tamaño de partícula es aproximadamente 1/100 del tamaño de partícula del cemento, lo que le confiere buenas propiedades de relleno. Además, el micropolvo de SiO₂, Al₂O₃, Cr₂O₃, etc., también puede formar partículas coloidales en agua. Cuando se utiliza un dispersante, se forma una doble capa eléctrica superpuesta sobre la superficie de las partículas para generar repulsión electrostática, lo que supera la fuerza de van der Waals entre ellas y reduce la energía de la interfaz. Esto evita la adsorción y la floculación entre partículas; al mismo tiempo, el dispersante se adsorbe alrededor de las partículas para formar una capa de disolvente, lo que también aumenta la fluidez del hormigón. Este es también uno de los mecanismos del polvo ultrafino: la adición de polvo ultrafino y dispersantes adecuados puede reducir el consumo de agua de los hormigónes refractarios y mejorar la fluidez.
El fraguado y endurecimiento de los hormigones refractarios con bajo contenido de cemento se debe a la acción combinada de la hidratación y la cohesión. La hidratación y el endurecimiento del cemento de aluminato de calcio se deben principalmente a la hidratación de las fases hidráulicas CA y CA₂ y al proceso de crecimiento cristalino de sus hidratos. Es decir, reaccionan con agua para formar escamas hexagonales o agujas de CAH₁₃ y C₂AH₃. Los productos de hidratación, como los cristales cúbicos de C₃AH₃ y los geles de Al₂O₃₂, forman una red interconectada de condensación-cristalización durante los procesos de curado y calentamiento. La aglomeración y la unión se deben a que el polvo ultrafino de SiO₂ activo forma partículas coloidales al entrar en contacto con el agua y con los iones que se disocian lentamente del aditivo añadido (es decir, la sustancia electrolítica). Debido a que las cargas superficiales de ambos son opuestas, es decir, la superficie coloidal ha adsorbido contraiones, el potencial β disminuye y se produce la condensación cuando la adsorción alcanza el punto isoeléctrico. En otras palabras, cuando la repulsión electrostática en la superficie de las partículas coloidales es menor que su atracción, se produce un enlace cohesivo mediante la fuerza de van der Waals. Tras la condensación del refractario fundido mezclado con polvo de sílice, los grupos Si-OH formados en la superficie del SiO₂ se secan y deshidratan para formar un puente, formando una estructura de red de siloxano (Si-O-Si), endureciéndose así. En la estructura de red de siloxano, los enlaces entre el silicio y el oxígeno no disminuyen con el aumento de la temperatura, por lo que la resistencia también continúa aumentando. Al mismo tiempo, a altas temperaturas, la estructura de red de SiO₂ reaccionará con el Al₂O₃ que la recubre para formar mullita, que puede mejorar la resistencia a temperaturas medias y altas.
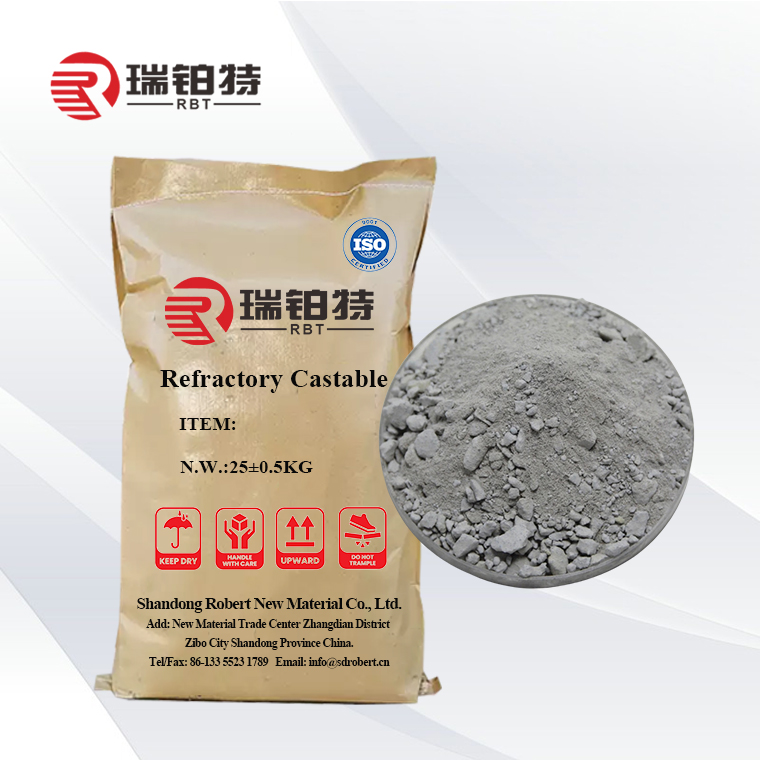
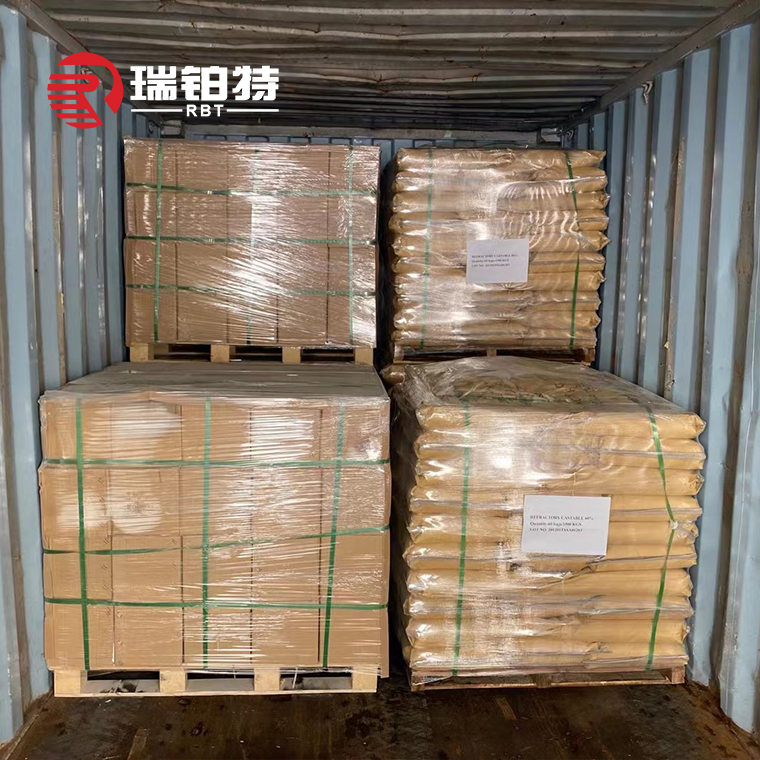
Hora de publicación: 28 de febrero de 2024