Exhibición del proceso de construcción de hormigón refractario en horno de cemento
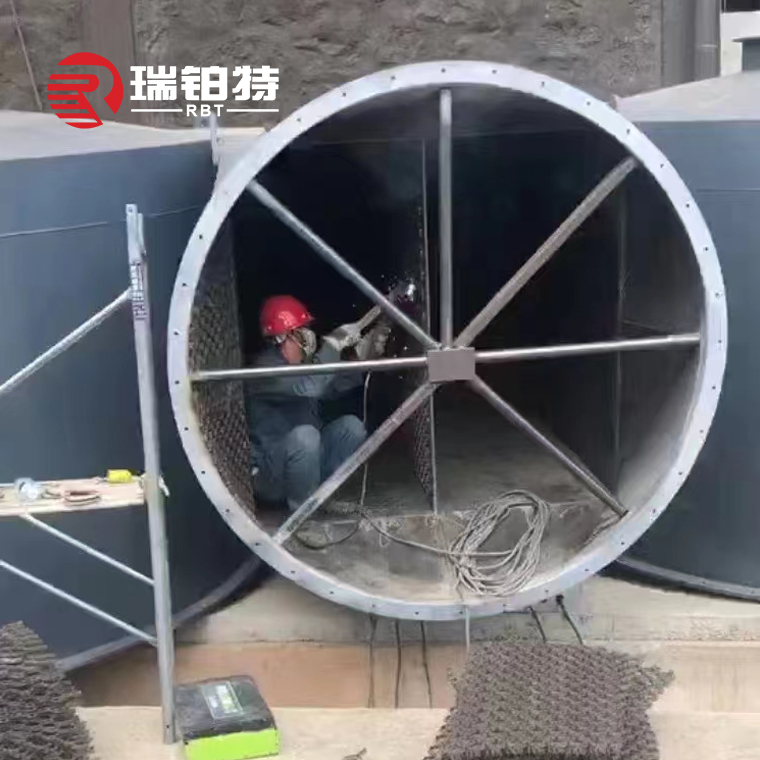
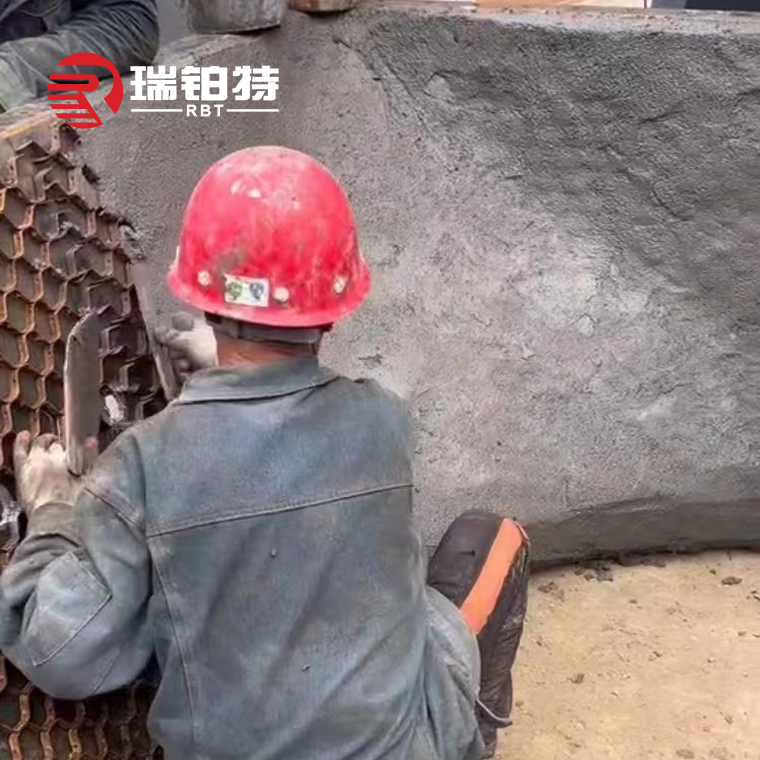
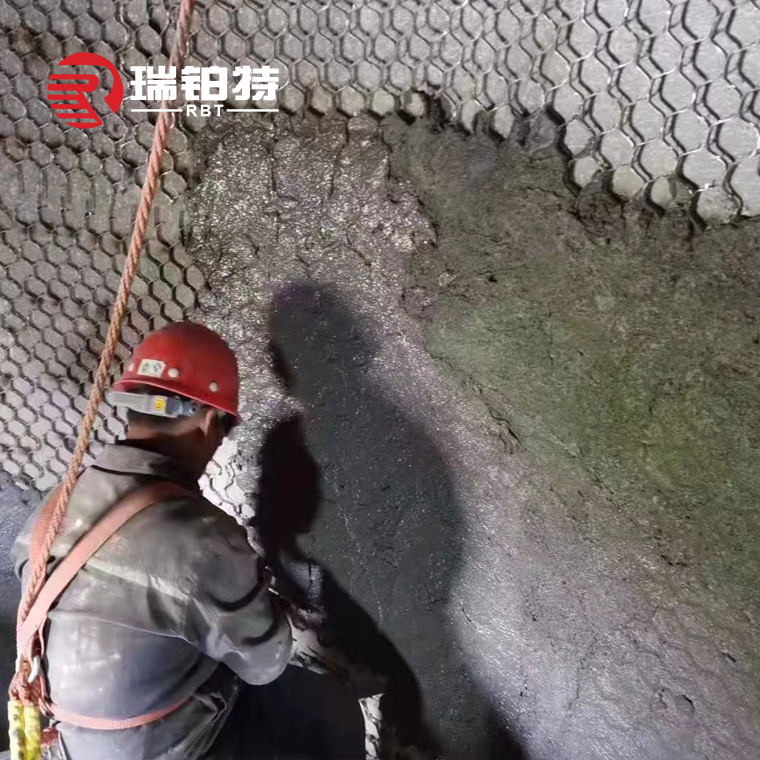
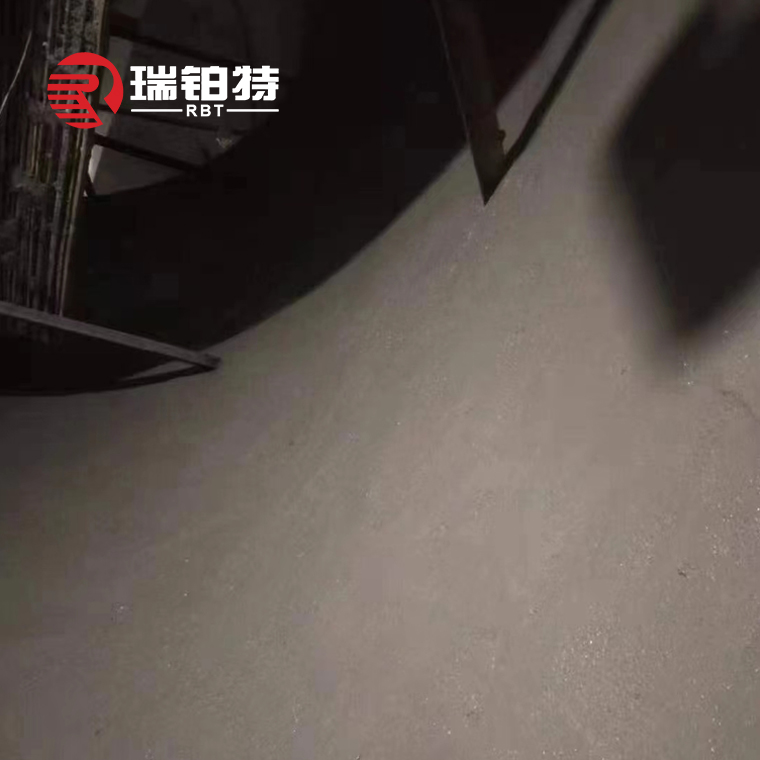
Hormigones refractarios para hornos rotatorios de cemento
1. Hormigones refractarios reforzados con fibra de acero para hornos de cemento
Los hormigones reforzados con fibra de acero incorporan principalmente fibras de acero inoxidable resistentes al calor, lo que les confiere mayor resistencia y resistencia al choque térmico, aumentando así su resistencia al desgaste y su vida útil. Este material se utiliza principalmente para piezas resistentes al desgaste a altas temperaturas, como bocas de horno, bocas de alimentación, pilares resistentes al desgaste y revestimientos de calderas de centrales eléctricas.
2. Hormigones refractarios de bajo contenido en cemento para hornos de cemento
Los hormigones refractarios de bajo contenido de cemento incluyen principalmente hormigones refractarios con alto contenido de alúmina, mullita y corindón. Esta serie de productos se caracteriza por su alta resistencia, resistencia a la abrasión, resistencia al desgaste y excelente rendimiento. Además, el material puede transformarse en hormigones a prueba de explosiones de cocción rápida, según los requisitos de tiempo de cocción del usuario.
3. Hormigones refractarios resistentes a los álcalis de alta resistencia para hornos de cemento
Los moldeables resistentes a los álcalis de alta resistencia presentan buena resistencia a la erosión por gases alcalinos y escorias, y una larga vida útil. Este material se utiliza principalmente para cubiertas de puertas de hornos, hornos de descomposición, sistemas de precalentamiento, sistemas de gestión, etc., y otros revestimientos de hornos industriales.
Método de construcción de hormigón colado con alto contenido de aluminio y bajo contenido de cemento para revestimiento de hornos rotatorios
La construcción de hormigón colado con alto contenido de aluminio y bajo contenido de cemento para revestimiento de hornos rotatorios requiere especial atención a los siguientes cinco procesos:
1. Determinación de juntas de expansión
Según la experiencia previa con el uso de hormigones con alto contenido de aluminio y bajo contenido de cemento, las juntas de expansión son un factor clave que afecta la vida útil de los revestimientos hormigonables de hornos rotatorios. Las juntas de expansión durante el vertido de los revestimientos de hornos rotatorios se determinan de la siguiente manera:
(1) Juntas circunferenciales: Secciones de 5 m, fieltro de fibra de silicato de aluminio de 20 mm intercalado entre los materiales refractarios y las fibras se compactan después de la expansión para amortiguar la tensión de expansión.
(2) Juntas planas: Cada tres tiras del hormigón se intercalan con madera contrachapada de 100 mm de profundidad en la dirección circunferencial interna y se deja una junta en el extremo de trabajo, para un total de 6 tiras.
(3) Durante el vertido, se utilizan 25 pasadores de escape por metro cuadrado para liberar una cierta cantidad de tensión de expansión mientras se vacía el horno.
2. Determinación de la temperatura de construcción
La temperatura de construcción ideal para hormigones con alto contenido de aluminio y bajo contenido de cemento es de 10 a 30 °C. Si la temperatura ambiente es baja, se deben tomar las siguientes medidas:
(1) Cierre el entorno de construcción circundante, agregue instalaciones de calefacción y evite estrictamente la congelación.
(2) Use agua caliente a 35-50 ℃ (determinado por la vibración de prueba de vertido en el sitio) para mezclar el material.
3. Mezclando
Determine la cantidad de mezcla de una vez según la capacidad del mezclador. Después de determinar la cantidad de mezcla, agregue el material de fundición en la bolsa y los aditivos de paquete pequeño en la bolsa en el mezclador al mismo tiempo. Primero, inicie el mezclador para mezclar en seco durante 2 a 3 minutos, luego agregue 4/5 del agua pesada primero, revuelva durante 2 a 3 minutos y luego determine el 1/5 restante del agua según la viscosidad del lodo. Después de mezclar completamente, se realiza un vertido de prueba y la cantidad de agua agregada se determina en combinación con la vibración y la situación de la lechada. Después de determinar la cantidad de agua agregada, debe controlarse estrictamente. Mientras se asegura que la lechada pueda vibrarse, se debe agregar la menor cantidad de agua posible (la cantidad de adición de agua de referencia para este material moldeable es del 5,5% al 6,2%).
4. Construcción
El tiempo de construcción del hormigón hormigonado con alto contenido de aluminio y bajo contenido de cemento es de aproximadamente 30 minutos. Los materiales deshidratados o condensados no se pueden mezclar con agua y deben desecharse. Utilice una varilla vibratoria para lograr la compactación de la lechada. La varilla vibratoria debe reservarse para evitar que la de repuesto se active si falla.
La construcción del material refractario debe realizarse en franjas a lo largo del eje del horno rotatorio. Antes de cada vertido, la superficie de construcción debe limpiarse para eliminar el polvo, la escoria de soldadura y otros residuos. Al mismo tiempo, verifique que la soldadura del anclaje y el tratamiento de pintura asfáltica de la superficie estén en su lugar. De lo contrario, se deben tomar medidas correctivas.
En la construcción de flejes, el cuerpo de colada debe vertidose abiertamente desde la cola del horno hasta el cabezal, en la parte inferior del cuerpo. El soporte de la plantilla debe colocarse entre el anclaje y la placa de acero. La placa de acero y el anclaje están firmemente incrustados con bloques de madera. El encofrado de soporte tiene una altura de 220 mm, un ancho de 620 mm, una longitud de 4-5 m y un ángulo central de 22,5°.
La construcción del segundo cuerpo de fundición debe realizarse después de que la tira esté finalmente fraguada y se retire el molde. Por un lado, se utiliza la plantilla arqueada para cerrar la fundición desde la cabeza del horno hasta la cola. El resto es similar.
Al vibrar el material de fundición, se debe añadir el lodo mezclado al molde del neumático durante la vibración. El tiempo de vibración debe controlarse para evitar burbujas visibles en la superficie del cuerpo de fundición. El tiempo de desmoldeo debe determinarse según la temperatura ambiente de la obra. Es necesario asegurar que el desmoldeo se realice una vez que el material de fundición haya fraguado y alcanzado cierta resistencia.
5. Horneado del revestimiento
La calidad de horneado del revestimiento del horno rotatorio afecta directamente su vida útil. En el proceso de horneado anterior, debido a la falta de experiencia madura y buenos métodos, se utilizó el método de inyección de aceite pesado para la combustión en los procesos de horneado de baja, media y alta temperatura. La temperatura era difícil de controlar: cuando la temperatura necesita ser controlada por debajo de 150 ℃, el aceite pesado no es fácil de quemar; cuando la temperatura es superior a 150 ℃, la velocidad de calentamiento es demasiado rápida y la distribución de la temperatura en el horno es muy desigual. La temperatura del revestimiento donde se quema el aceite pesado es aproximadamente 350~500 ℃ más alta, mientras que la temperatura de otras partes es baja. De esta manera, el revestimiento es fácil de reventar (el revestimiento moldeable anterior se ha reventado durante el proceso de horneado), lo que afecta su vida útil.
Hora de publicación: 10 de julio de 2024