Las causas de las grietas en los hormigones durante la cocción son relativamente complejas e involucran la velocidad de calentamiento, la calidad del material, la tecnología de construcción y otros aspectos. A continuación, se presenta un análisis específico de las causas y sus soluciones:
1. La velocidad de calentamiento es demasiado rápida
Razón:
Durante el proceso de horneado de los moldeables, si la velocidad de calentamiento es demasiado rápida, el agua interna se evapora rápidamente y la presión de vapor generada es alta. Si esta supera la resistencia a la tracción del moldeable, se producirán grietas.
Solución:
Desarrolle una curva de horneado razonable y controle la velocidad de calentamiento según factores como el tipo y el grosor del material moldeable. En general, la etapa inicial de calentamiento debe ser lenta, preferiblemente sin superar los 50 °C/h. A medida que la temperatura aumenta, la velocidad de calentamiento puede acelerarse adecuadamente, pero también debe controlarse entre 100 °C/h y 150 °C/h. Durante el proceso de horneado, utilice un registrador de temperatura para monitorear los cambios de temperatura en tiempo real y garantizar que la velocidad de calentamiento cumpla con los requisitos.
2. Problema de calidad del material
Razón:
Relación inadecuada de agregado y polvo: si hay demasiados agregados y polvo insuficiente, el rendimiento de unión del material moldeable disminuirá y aparecerán grietas fácilmente durante la cocción; por el contrario, demasiado polvo aumentará la tasa de contracción del material moldeable y también provocará fácilmente grietas.
Uso inadecuado de aditivos: El tipo y la cantidad de aditivos influyen significativamente en el rendimiento del material moldeable. Por ejemplo, el uso excesivo de reductor de agua puede causar una excesiva fluidez del material moldeable, lo que provoca segregación durante la solidificación y la aparición de grietas durante el horneado.
Solución:
Controlar rigurosamente la calidad de las materias primas y pesar con precisión materiales como agregados, polvos y aditivos, según los requisitos de la fórmula del fabricante. Inspeccionar y cribar periódicamente las materias primas para garantizar que el tamaño de partícula, la granulometría y la composición química cumplan con los requisitos.
Para nuevos lotes de materias primas, primero realice una pequeña prueba de muestra para probar el rendimiento del material moldeable, como fluidez, resistencia, contracción, etc., ajuste la fórmula y la dosis de aditivos de acuerdo con los resultados de la prueba y luego úselos a gran escala después de que estén calificados.
3. Problemas del proceso de construcción
Razones:
Mezcla desigual:Si el material moldeable no se mezcla de manera uniforme durante el mezclado, el agua y los aditivos que contiene se distribuirán de manera desigual y se producirán grietas durante el horneado debido a las diferencias de rendimiento en las diferentes partes.
Vibración no compactada: Durante el proceso de vertido, la vibración no compactada provocará poros y huecos dentro del material moldeable, y estas partes débiles son propensas a agrietarse durante el horneado.
Mantenimiento inadecuado:Si el agua en la superficie del hormigón no se mantiene completamente después del vertido, el agua se evapora demasiado rápido, lo que provocará una contracción excesiva de la superficie y grietas.
Solución:
Utilice una mezcladora mecánica y controle estrictamente el tiempo de mezclado. Generalmente, el tiempo de mezclado de una mezcladora forzada no es inferior a 3-5 minutos para garantizar una mezcla uniforme del material. Durante el proceso de mezclado, añada la cantidad adecuada de agua para que el material alcance la fluidez adecuada.
Al vibrar, utilice herramientas adecuadas, como varillas vibratorias, etc., y vibre en un orden y espaciado determinados para asegurar la densidad del material. El tiempo de vibración debe ser adecuado para evitar burbujas y hundimientos en la superficie del material.
Tras el vertido, el curado debe realizarse a tiempo. Se pueden utilizar películas plásticas, esteras de paja húmeda y otros métodos para mantener húmeda la superficie del hormigón. El tiempo de curado no suele ser inferior a 7-10 días. Para hormigón de gran volumen o hormigón construido en entornos de alta temperatura, también se puede utilizar el curado por aspersión y otras medidas.
4. Problema del entorno de horneado
Causa:
La temperatura ambiente es demasiado baja:Al hornear en un entorno de baja temperatura, la velocidad de solidificación y secado del material moldeable es lenta y es fácil que se congele, lo que provoca daños estructurales internos y, por lo tanto, grietas.
Mala ventilación:Durante el proceso de horneado, si la ventilación no es uniforme, el agua evaporada del interior del material moldeable no puede descargarse a tiempo y se acumula en el interior formando alta presión, lo que provoca grietas.
Solución:
Cuando la temperatura ambiente sea inferior a 5 °C, se deben tomar medidas de calentamiento, como usar un calentador, una tubería de vapor, etc., para precalentar el ambiente de horneado, de modo que la temperatura ambiente supere los 10-15 °C antes de hornear. Durante el horneado, la temperatura ambiente también debe mantenerse estable para evitar fluctuaciones excesivas de temperatura.
Configure las rejillas de ventilación de forma adecuada para garantizar una buena ventilación durante el horneado. Según el tamaño y la forma del equipo, se pueden instalar varias rejillas, cuyo tamaño se puede ajustar según sea necesario para garantizar una evacuación fluida de la humedad. Al mismo tiempo, evite colocar el material refractario directamente sobre las rejillas para evitar grietas debido al secado excesivo del aire.
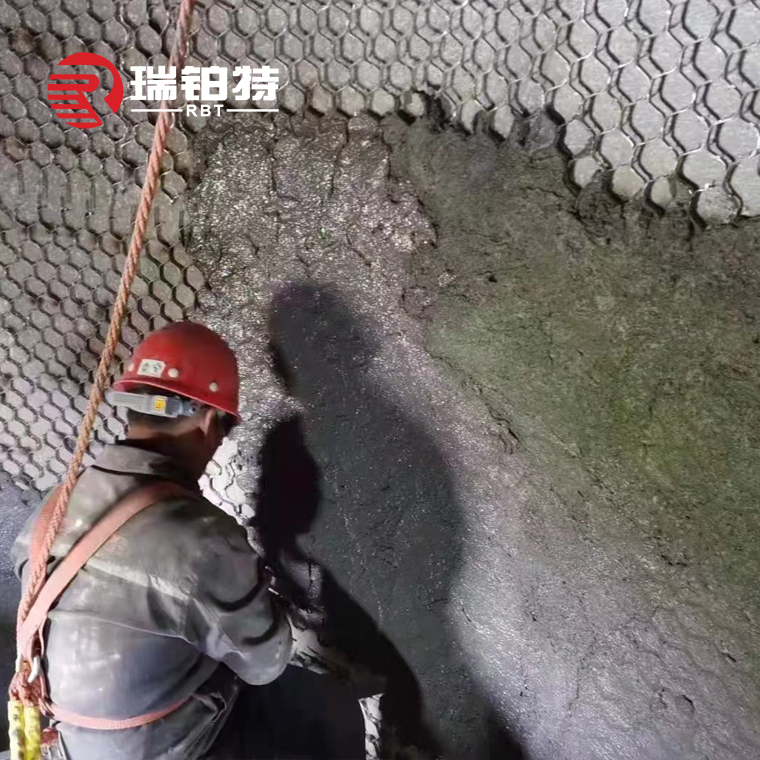
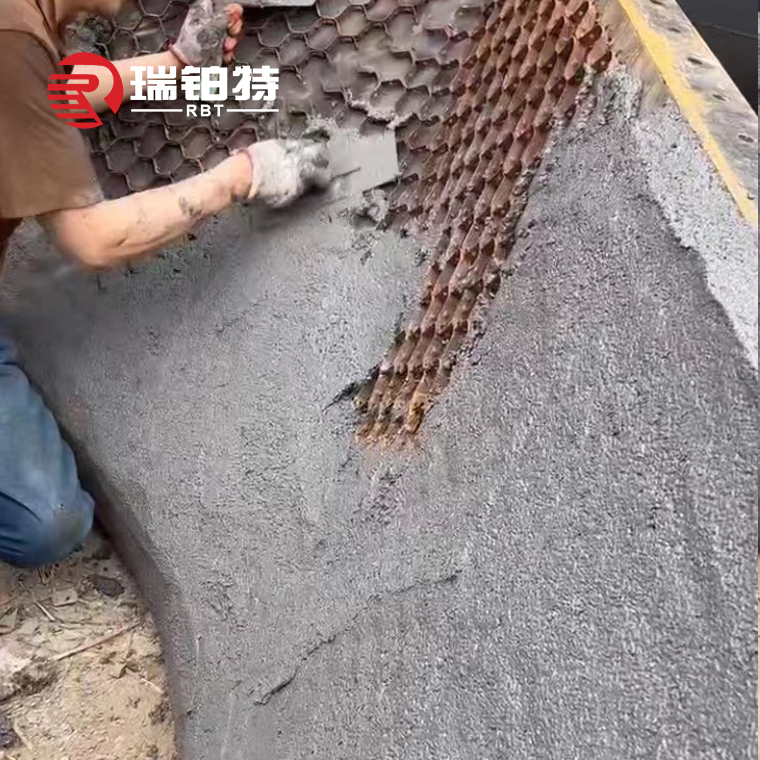
Hora de publicación: 07-05-2025